En la industria de la granulación, ya sea una máquina de pellets plano o una máquina de pellets de matriz de anillo, su principio de funcionamiento es confiar en el movimiento relativo entre la azahada de presión y el molde para agarrar el material y ingresar a la estación efectiva, extruirlo en forma y luego cortarlo en partículas de la longitud requerida por la cuchilla de corte.
Carcasa de rodillo de prensa de partículas
La carcasa del rodillo de presión incluye principalmente un eje excéntrico, rodamientos de rodillos, una cubierta de rodillo de presión con manga fuera del eje del rodillo de presión y componentes utilizados para soportar y fijar la cubierta del rodillo de presión.
La capa de presión de presión apreta el material en el orificio del molde y lo forma bajo presión en el orificio del molde. Para evitar que el rodillo de presión se deslice y aumente la fuerza de agarre, debe haber una cierta fuerza de fricción entre el rodillo de presión y el material. Por lo tanto, las medidas para aumentar la fricción y la resistencia al desgaste a menudo se toman en la superficie del rodillo de presión. Cuando se determinan los parámetros estructurales del rodillo de presión y el moho, la forma estructural y el tamaño de la superficie externa del rodillo de presión tienen un impacto significativo en la eficiencia de la granulación y la calidad de las partículas.
Estructura de la superficie de la carcasa del rodillo de presión
Hay tres tipos comunes de superficie para los rodillos de prensa de partículas existentes: superficie de rodillo ranurado, superficie de rodillo ranurado con sellado de borde y superficie del rodillo de panal.
El rodillo de presión de tipo de ranura dentada tiene un buen rendimiento de rodadura y se usa ampliamente en las fábricas de alimentación de ganado y aves de corral. Sin embargo, debido al deslizamiento de la alimentación en la ranura dentada, el desgaste del rodillo de presión y el molde del anillo no es muy uniforme, y el desgaste en ambos extremos del rodillo de presión y el molde del anillo es más severo.
El rodillo de presión de tipo de ranura dentada con sellado de borde es principalmente adecuado para la producción de materiales acuáticos. Los materiales acuáticos son más propensos a deslizarse durante la extrusión. Debido al sellado de borde en ambos lados de la ranura dentada, no es fácil deslizarse hacia ambos lados durante la extrusión de alimentación, lo que resulta en una distribución más uniforme de la alimentación. El desgaste del rodillo de presión y el molde del anillo también es más uniforme, lo que resulta en una longitud más consistente de los gránulos producidos.
La ventaja del rodillo de panal es que el desgaste del molde del anillo es uniforme, y la longitud de las partículas producidas también es relativamente consistente. Sin embargo, el rendimiento de la bobina es deficiente, lo que afecta la salida del granulador y no es tan común como el uso del tipo de ranura en la producción real.
El siguiente es un resumen de 10 tipos de rodillos de presión de máquina de partículas para moldes de anillo de rodillos de presión de Baoshell, ¡y los últimos 3 son definitivamente los que no has visto!
Tipo de ranura No.10
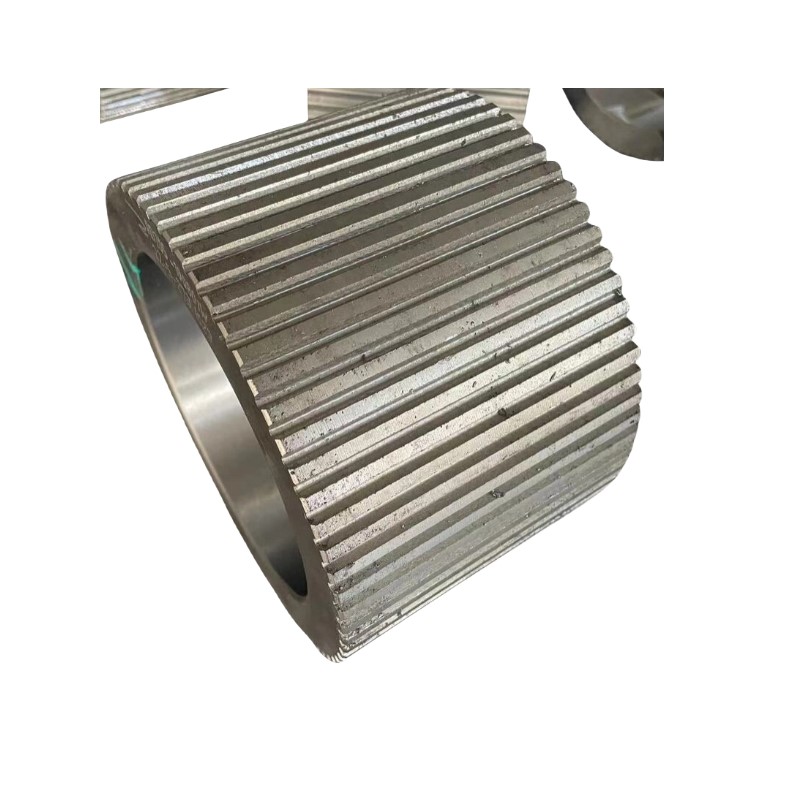
No.9 Tipo de ranura cerrada
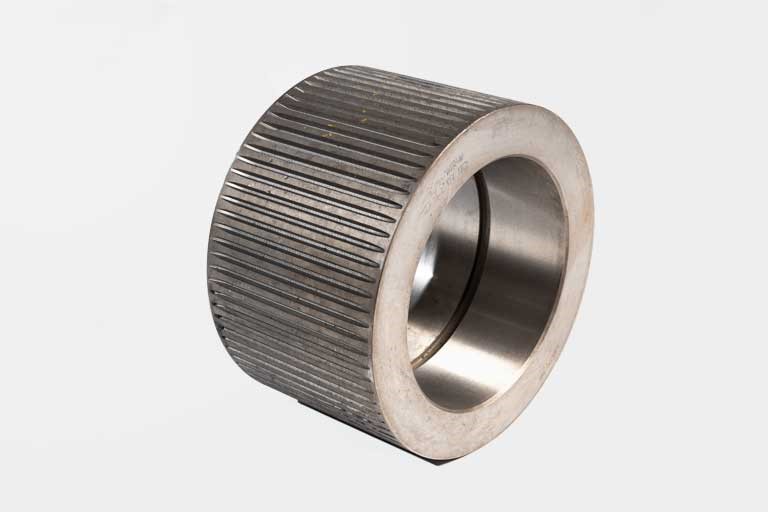
No.8 Tipo de panal
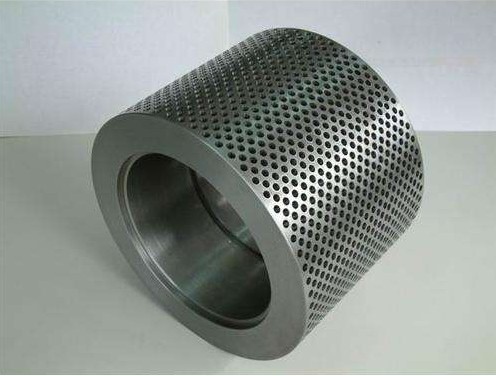
No.7 en forma de diamante
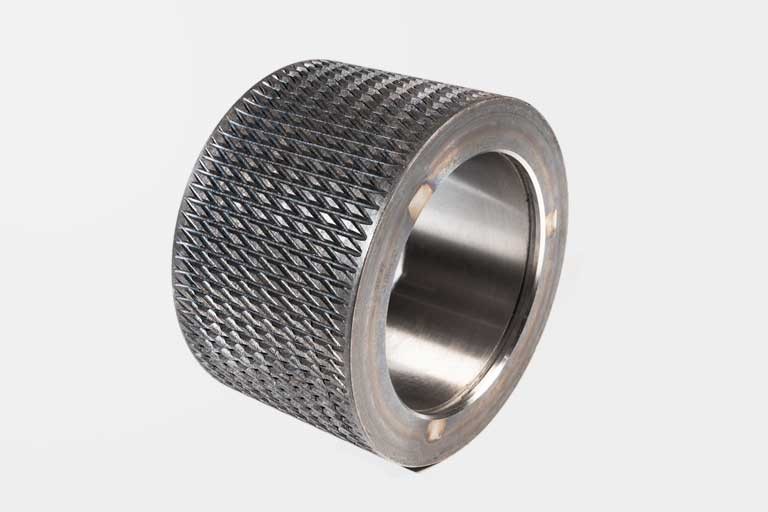
No.6 Groove inclinado
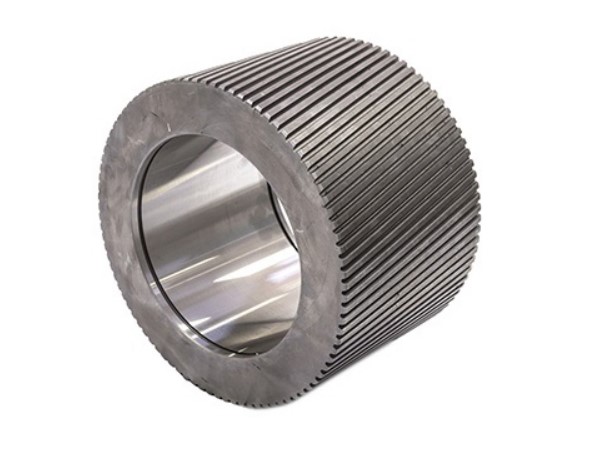
No.5 Groove+Honeycomb
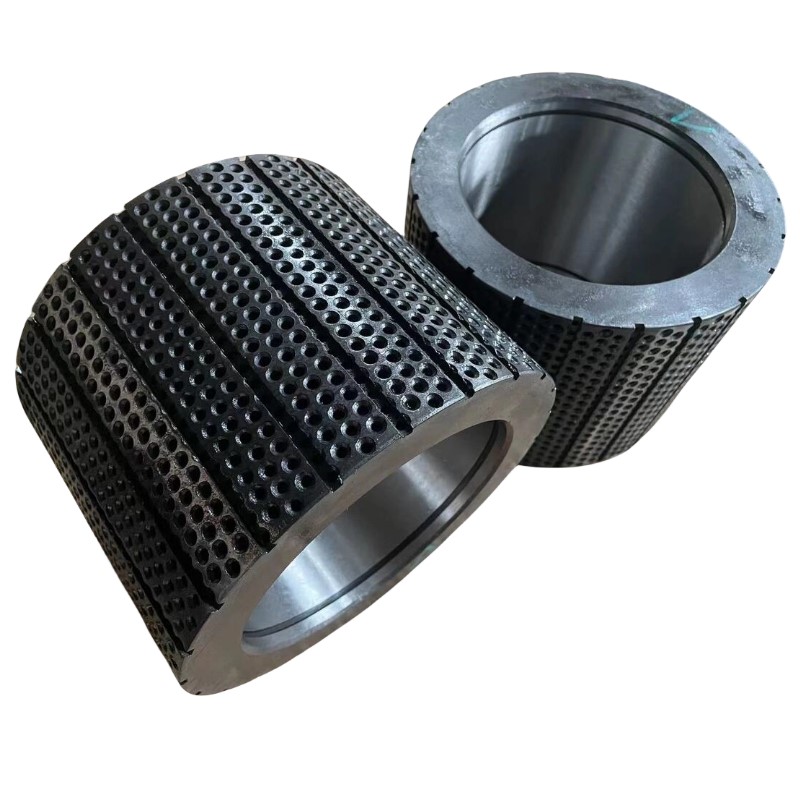
No.4 Groove cerrado+Honeycomb
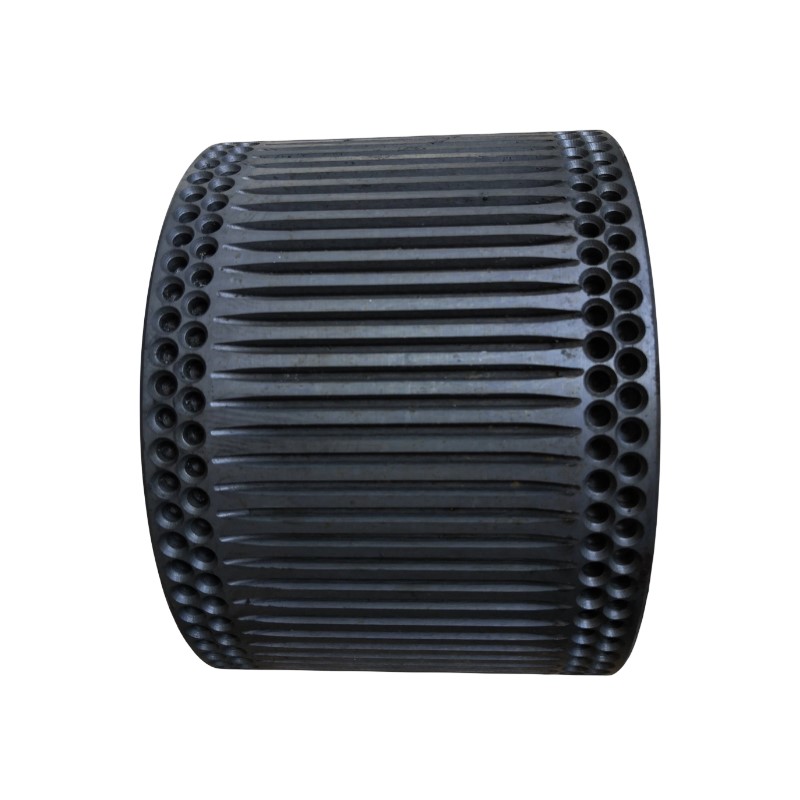
No.3 Groove inclinado+Honeycomb
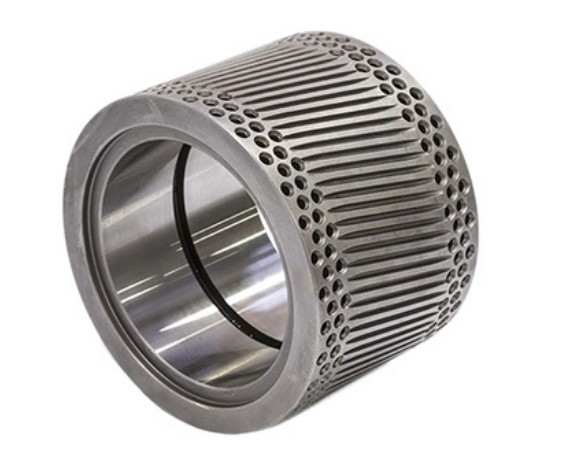
No.2 Pescado de huesos
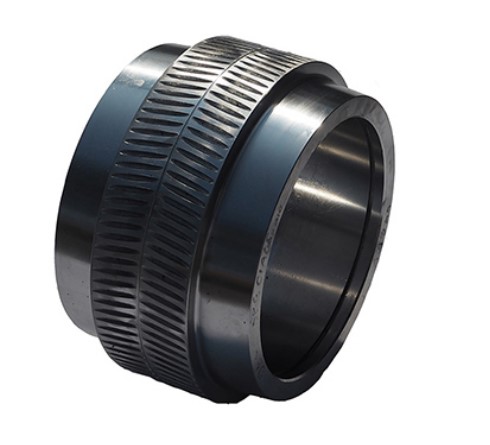
No.1 onda en forma de arco
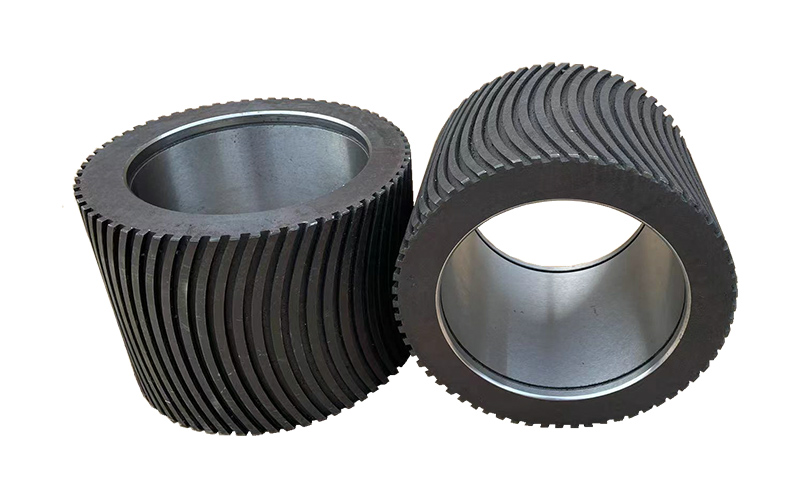
Modelo seppecial: caparazón de tungsteno carburo
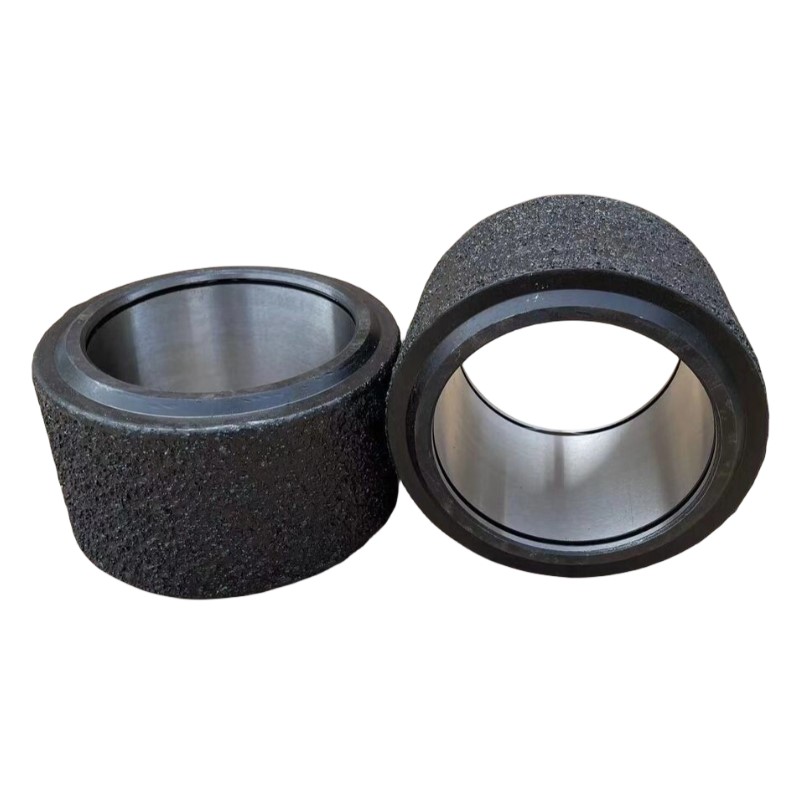
El método de tratamiento para el deslizamiento del rodillo de presión de la máquina de partículas
Debido al entorno de trabajo duro, la alta intensidad de trabajo y la velocidad de desgaste rápida de la carcasa del rodillo de presión, el rodillo de presión es una parte vulnerable de la máquina de partículas y debe reemplazarse regularmente. La práctica de producción ha demostrado que mientras las características de los materiales de producción cambien u otras condiciones cambien durante el procesamiento, puede ocurrir el fenómeno del deslizamiento del rodillo de presión de la máquina de partículas. Si hay un deslizamiento del rodillo de presión durante el proceso de granulación, no se asuste. Para obtener detalles específicos, consulte las siguientes técnicas:
Razón 1: Mala concentricidad del rodillo de presión y la instalación del huso
Solución:
Verifique si la instalación de los rodamientos de rodillos de presión es razonable para evitar que la carcasa del rodillo de presión se desvíe a un lado.
Razón 2: La boca de la campana del molde del anillo es molido plano, lo que hace que el moho no coma materiales
Solución:
Verifique el desgaste de las abrazaderas, las ruedas de transmisión y los anillos de revestimiento del granulador.
Ajuste la concentricidad de la instalación del molde del anillo, con un error que no exceda de 0.3 mm.
La brecha entre los rodillos de presión debe ajustarse a: la mitad de la superficie de trabajo de los rodillos de presión está funcionando con el molde, y la rueda de ajuste y el tornillo de bloqueo también se debe garantizar que esté en buenas condiciones de trabajo.
Cuando el rodillo de presión se deslice, no permita que la máquina de partículas se inactive durante mucho tiempo y espere a que descargue el material por sí solo.
La relación de compresión de la apertura del molde del anillo utilizada es demasiado alta, lo que causa una alta resistencia al material de material del moho y también es una de las razones para el deslizamiento del rodillo de presión.
No se debe permitir que la máquina de pellet se inactive innecesariamente sin alimentación de material.
Razón 3: El rodamiento de rodillos de presión está atascado
Solución:
Reemplace los cojinetes de rodillo de presión.
Razón 4: La carcasa del rodillo de presión no es redonda
Solución:
La calidad de la carcasa del rodillo no está calificada, reemplaza o repara la carcasa del rodillo.
Cuando el rodillo de presión se desliza, debe detenerse de manera oportuna para evitar la fricción inactiva prolongada del rodillo de presión.
Razón 5: flexión o aflojamiento del huso del rodillo de presión
Solución:
Reemplace o apriete el huso y verifique la condición del husillo del rodillo de presión al reemplazar el molde del anillo y el rodillo de presión.
Razón 6: La superficie de trabajo del rodillo de presión está relativamente desalineada con la superficie de trabajo del molde del anillo (cruce de borde)
Solución:
Verifique si el rodillo de presión está instalado de manera incorrecta y reemplácelo.
Verifique si el eje excéntrico del rodillo de presión está deformado.
Verifique el desgaste en los cojinetes del eje principal o los bujes de la máquina de partículas.
Razón 7: El espacio libre del huso del granulador es demasiado grande
Solución:
Verifique el espacio libre del granulador.
Razón 8: La tasa de perforación del molde del anillo es baja (menos del 98%)
Solución:
Use un taladro de pistola para perforar a través del orificio del molde, o hervirlo en aceite, mértelo antes de alimentarse.
Razón 9: las materias primas son demasiado gruesas y tienen alto contenido de humedad
Solución:
Presta atención a mantener un contenido de humedad de aproximadamente el 15%. Si el contenido de humedad de las materias primas es demasiado alto, habrá bloqueo de moho y deslizamiento después de que las materias primas ingresen al molde del anillo. El rango de control de humedad de las materias primas es entre 13-20%.
Razón 10: Nuevo alimentación de moho demasiado rápido
Solución:
Ajuste la velocidad para garantizar que el rodillo de presión tenga suficiente tracción, evite que el rodillo de presión se deslice y verifique rápidamente el desgaste del molde del anillo y el rodillo de presión.
Tiempo de publicación: marzo-25-2024