Debido a la menor cantidad de sustancias nocivas, como cenizas, nitrógeno y azufre, en la biomasa, en comparación con la energía mineral, esta se caracteriza por sus grandes reservas, buena actividad de carbono, fácil ignición y alta volatilidad. Por lo tanto, la biomasa es un combustible energético ideal, ideal para la conversión y utilización de la combustión. Las cenizas residuales tras la combustión de la biomasa son ricas en nutrientes esenciales para las plantas, como fósforo, calcio, potasio y magnesio, por lo que pueden utilizarse como fertilizante para su retorno al campo. Dadas las enormes reservas de recursos y las ventajas únicas de las energías renovables, la biomasa se considera actualmente una opción importante para el desarrollo de nuevas energías a nivel nacional en países de todo el mundo. La Comisión Nacional de Desarrollo y Reforma de China ha declarado claramente en el "Plan de Implementación para la Utilización Integral de la Paja de Cultivos durante el XII Plan Quinquenal" que la tasa de utilización integral de la paja alcanzará el 75 % para 2013 y aspira a superar el 80 % para 2015.
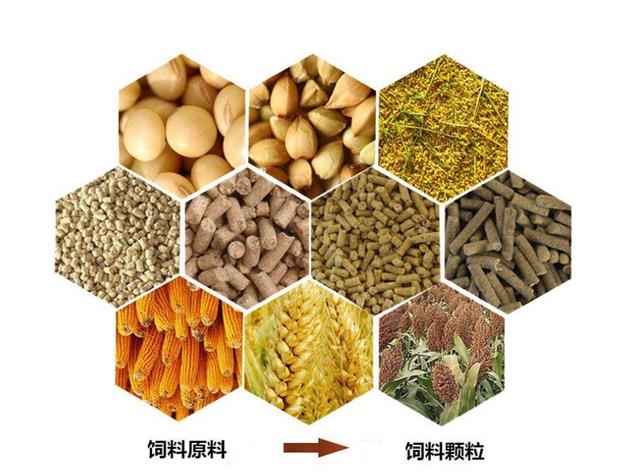
Cómo convertir la energía de biomasa en energía limpia, de alta calidad y conveniente se ha convertido en un problema urgente. La tecnología de densificación de biomasa es una de las maneras más efectivas de mejorar la eficiencia de la incineración de biomasa y facilitar su transporte. Actualmente, existen cuatro tipos comunes de equipos de conformado denso en el mercado nacional e internacional: la máquina de extrusión de partículas en espiral, la máquina de estampado de partículas por pistón, la máquina de molde plano y la máquina de molde anular. Entre ellas, la máquina de pellets con molde anular es ampliamente utilizada debido a sus características, como la ausencia de calentamiento durante su funcionamiento, los amplios requisitos de contenido de humedad de la materia prima (del 10 % al 30 %), la alta producción individual, la alta densidad de compresión y el buen rendimiento de conformado. Sin embargo, este tipo de máquinas de pellets generalmente presenta desventajas como el fácil desgaste del molde, la corta vida útil, los altos costos de mantenimiento y la incomodidad de su reemplazo. Para abordar las deficiencias mencionadas de la máquina de pellets con molde anular, el autor ha implementado un diseño completamente nuevo y mejorado en la estructura del molde de conformado, diseñando un molde de conformado de tipo fijo con una larga vida útil, bajo costo de mantenimiento y un mantenimiento conveniente. Mientras tanto, este artículo realizó un análisis mecánico del molde de formación durante su proceso de trabajo.
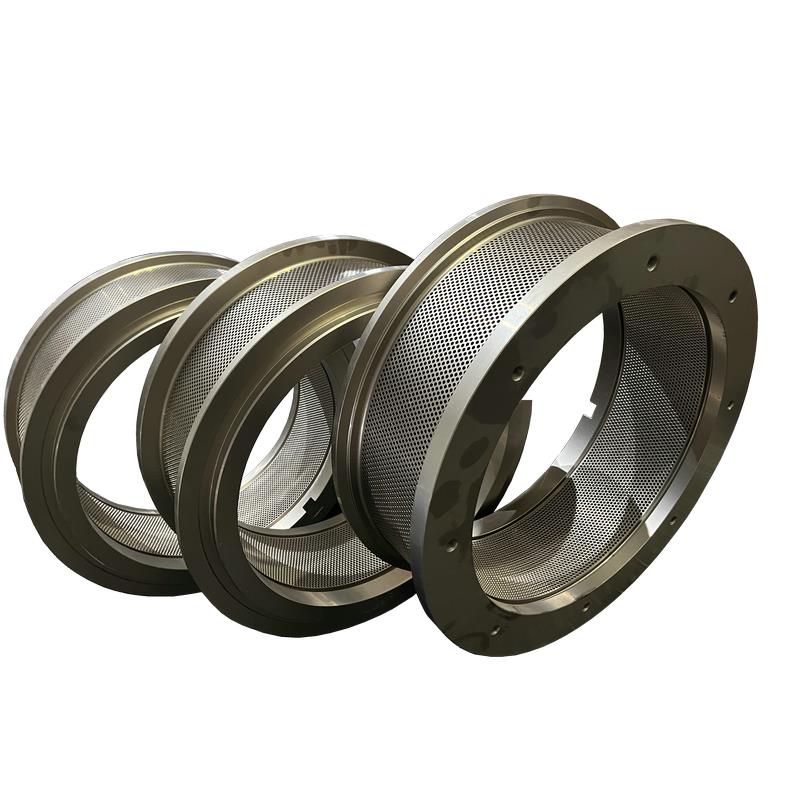
1. Diseño mejorado de la estructura del molde de conformación para granulador de molde anular
1.1 Introducción al proceso de conformado por extrusión:La peletizadora con matriz anular se puede dividir en dos tipos: vertical y horizontal, según la posición de la matriz anular. Según su movimiento, se puede dividir en dos: rodillo de presión activo con molde anular fijo y rodillo de presión activo con molde anular accionado. Este diseño mejorado está dirigido principalmente a la peletizadora con molde anular con rodillo de presión activo y molde anular fijo como mecanismo de movimiento. Consta principalmente de dos partes: un mecanismo de transporte y un mecanismo de partícula con molde anular. El molde anular y el rodillo de presión son los dos componentes principales de la peletizadora con molde anular, con numerosos orificios de formación distribuidos alrededor del molde anular, y el rodillo de presión está instalado en su interior. El rodillo de presión está conectado al husillo de transmisión, y el molde anular está instalado en un soporte fijo. Cuando el husillo gira, impulsa el rodillo de presión. Principio de funcionamiento: En primer lugar, el mecanismo de transporte transporta la biomasa triturada en partículas de un tamaño determinado (3-5 mm) a la cámara de compresión. Luego, el motor acciona el eje principal para impulsar la rotación del rodillo de presión, y el rodillo de presión se mueve a una velocidad constante para dispersar uniformemente el material entre el rodillo de presión y el molde anular, provocando que el molde anular se comprima y friccione con el material, el rodillo de presión con el material y el material con el material. Durante el proceso de compresión por fricción, la celulosa y la hemicelulosa del material se combinan entre sí. Al mismo tiempo, el calor generado por la fricción de compresión ablanda la lignina en un aglutinante natural, lo que hace que la celulosa, la hemicelulosa y otros componentes se unan más firmemente. Con el llenado continuo de materiales de biomasa, la cantidad de material sometido a compresión y fricción en los orificios del molde de formación continúa aumentando. Al mismo tiempo, la fuerza de compresión entre la biomasa continúa aumentando y se densifica y forma continuamente en el orificio de moldeo. Cuando la presión de extrusión es mayor que la fuerza de fricción, la biomasa se extruye de manera continua desde los orificios de moldeo alrededor del molde anular, formando combustible de moldeo de biomasa con una densidad de moldeo de aproximadamente 1 g/cm3.
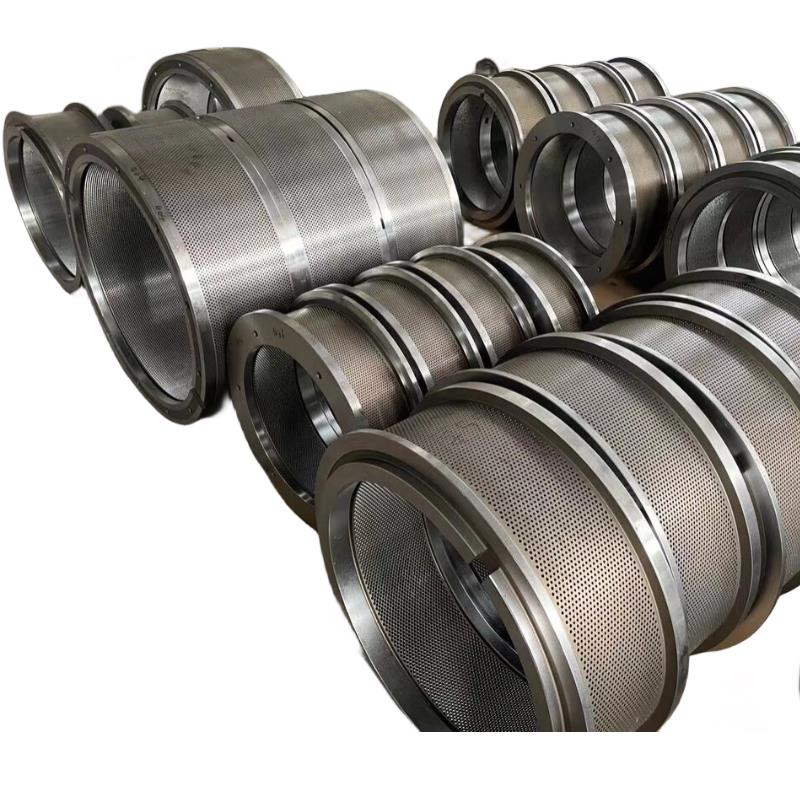
1.2 Desgaste de los moldes de conformación:La peletizadora de molde anular tiene una gran capacidad de producción, un alto grado de automatización y una gran adaptabilidad a las materias primas. Es ampliamente utilizada para procesar diversas materias primas de biomasa, lo que la hace adecuada para la producción a gran escala de combustibles de biomasa densos y satisface las futuras necesidades de industrialización de estos combustibles. Por lo tanto, la peletizadora de molde anular es ampliamente utilizada. Debido a la posible presencia de pequeñas cantidades de arena y otras impurezas no derivadas de la biomasa en el material de biomasa procesado, es muy probable que se produzca un desgaste significativo en el molde anular de la peletizadora. La vida útil del molde anular se calcula en función de la capacidad de producción. Actualmente, la vida útil del molde anular en China es de tan solo 100-1000 toneladas.
La falla del molde de anillo ocurre principalmente en los siguientes cuatro fenómenos: ① Después de que el molde de anillo funciona durante un período de tiempo, la pared interna del orificio del molde de formación se desgasta y la abertura aumenta, lo que resulta en una deformación significativa del combustible formado producido; ② La pendiente de alimentación del orificio de la matriz de formación del molde de anillo se desgasta, lo que resulta en una disminución en la cantidad de material de biomasa comprimido en el orificio de la matriz, una disminución en la presión de extrusión y un fácil bloqueo del orificio de la matriz de formación, lo que lleva a la falla del molde de anillo (Figura 2); ③ Después de los materiales de la pared interna y reduce drásticamente la cantidad de descarga (Figura 3);
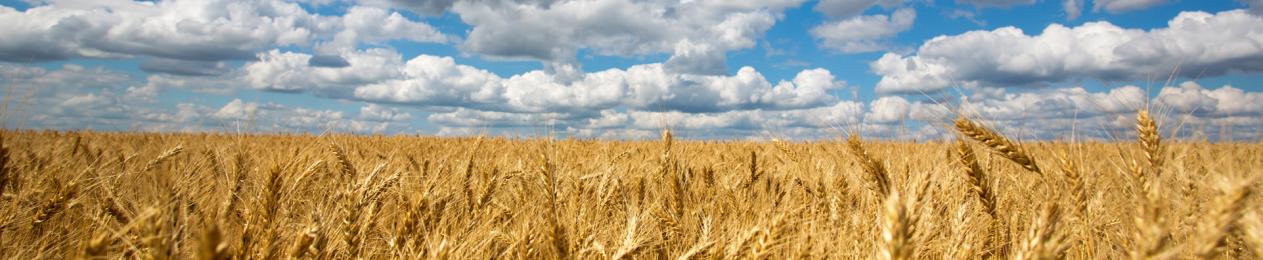
④ Tras el desgaste del orificio interior del molde anular, el espesor de la pared entre las piezas adyacentes L disminuye, lo que reduce su resistencia estructural. Es probable que se produzcan grietas en la sección más peligrosa y, a medida que estas se extienden, se produce la fractura del molde anular. La principal razón del fácil desgaste y la corta vida útil del molde anular es la estructura inadecuada del molde (el molde anular está integrado con los orificios del molde). Esta estructura integrada tiende a estos resultados: a veces, cuando solo algunos orificios del molde anular están desgastados y no funcionan, es necesario reemplazar todo el molde anular, lo que no solo genera inconvenientes en el trabajo de reemplazo, sino que también genera un gran desperdicio económico y aumenta los costos de mantenimiento.
1.3 Diseño de mejora estructural del molde de conformadoPara prolongar la vida útil del molde anular de la peletizadora, reducir el desgaste, facilitar su reemplazo y reducir los costos de mantenimiento, es necesario implementar un nuevo diseño mejorado en su estructura. Se utilizó un molde de moldeo integrado, y la estructura mejorada de la cámara de compresión se muestra en la Figura 4. La Figura 5 muestra la vista en sección transversal del molde de moldeo mejorado.
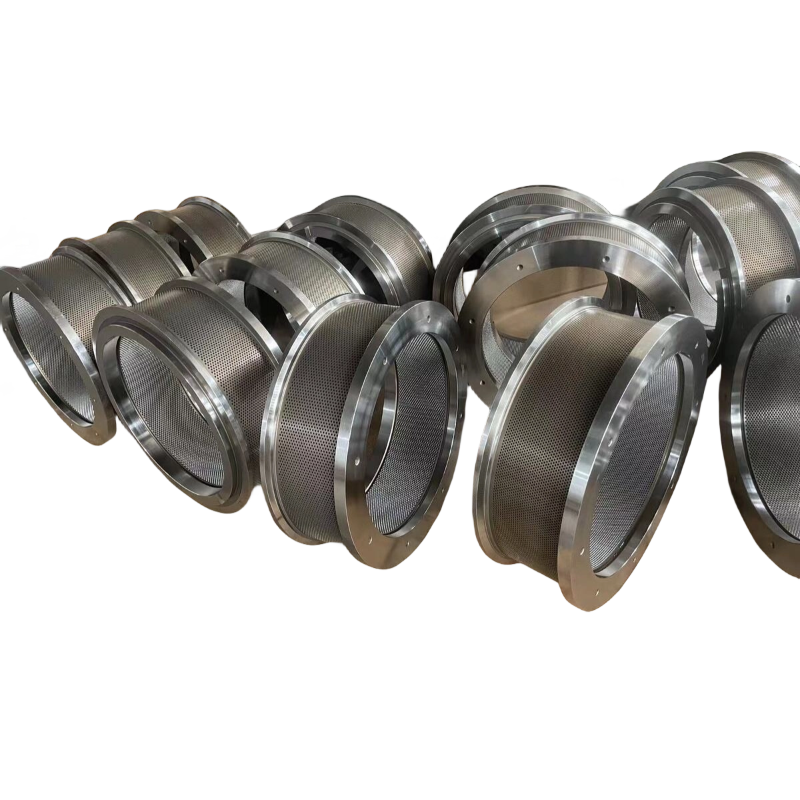
Este diseño mejorado está dirigido principalmente a la máquina de moldeo de partículas con anillo, con un rodillo de presión activo y un molde de anillo fijo. El molde de anillo inferior está fijado al cuerpo, y los dos rodillos de presión están conectados al eje principal mediante una placa de conexión. El molde de conformación está integrado en el molde de anillo inferior (mediante ajuste por interferencia), y el molde de anillo superior se fija al molde de anillo inferior mediante pernos y se sujeta al molde de conformación. Al mismo tiempo, para evitar que el molde de conformación rebote debido a la fuerza después de que el rodillo de presión gire y se mueva radialmente a lo largo del molde de anillo, se utilizan tornillos avellanados para fijar el molde de conformación a los moldes de anillo superior e inferior, respectivamente. Para reducir la resistencia del material que entra en el orificio y facilitar su entrada, el ángulo cónico del orificio de alimentación del molde de conformación diseñado es de 60° a 120°.
El diseño estructural mejorado del molde de conformado se caracteriza por su capacidad para múltiples ciclos y una larga vida útil. Cuando la máquina de partículas funciona durante un tiempo, la pérdida de fricción provoca que la abertura del molde de conformado se agrande y se pasifique. Al retirar y expandir el molde de conformado desgastado, se puede utilizar para la producción de otras especificaciones de partículas de conformado. Esto permite la reutilización de moldes y ahorra costos de mantenimiento y reemplazo.
Para prolongar la vida útil del granulador y reducir los costos de producción, el rodillo de presión utiliza acero con alto contenido de carbono y manganeso, como el 65Mn, con buena resistencia al desgaste. El molde de conformado debe estar hecho de acero carburizado aleado o de aleación de níquel-cromo con bajo contenido de carbono, como Cr, Mn, Ti, etc. Gracias a la mejora de la cámara de compresión, la fuerza de fricción que experimentan los moldes de anillo superior e inferior durante la operación es relativamente baja en comparación con el molde de conformado. Por lo tanto, se puede utilizar acero al carbono común, como el acero 45, como material para la cámara de compresión. En comparación con los moldes de anillo de conformado integrados tradicionales, se puede reducir el uso de aceros aleados de alto costo, lo que disminuye los costos de producción.
2. Análisis mecánico del molde de formación de la máquina de pellets de molde anular durante el proceso de trabajo del molde de formación.
Durante el proceso de moldeo, la lignina del material se ablanda por completo debido al ambiente de alta presión y temperatura generado en el molde. Cuando la presión de extrusión no aumenta, el material se plastifica. El material fluye bien después de la plastificación, por lo que la longitud se puede ajustar a d. El molde de conformación se considera un recipiente a presión, lo que simplifica la tensión sobre él.
Del análisis de cálculo mecánico anterior, se concluye que, para obtener la presión en cualquier punto del molde, es necesario determinar la deformación circunferencial en ese punto. Posteriormente, se calculan la fuerza de fricción y la presión en ese punto.
3. Conclusión
Este artículo propone un nuevo diseño de mejora estructural para el molde de conformación de la peletizadora de molde anular. El uso de moldes de conformación integrados puede reducir eficazmente el desgaste del molde, prolongar su vida útil, facilitar su reemplazo y mantenimiento, y reducir los costos de producción. Simultáneamente, se realizó un análisis mecánico del molde de conformación durante su proceso de trabajo, lo que proporciona una base teórica para futuras investigaciones.
Hora de publicación: 22 de febrero de 2024